Radiated Emissions Testing: A Step-by-Step Guide to Compliance and Reliability
What is Radiated Emissions Testing?
Radiated emissions testing is a crucial process in the field of electromagnetic compatibility (EMC) that assesses the electromagnetic interference (EMI) produced by electronic devices and systems. This testing aims to ensure that devices do not emit excessive electromagnetic energy that could potentially disrupt the performance of nearby electronic equipment. It is essential for manufacturers to understand the components, methodology, and implications associated with radiated emissions to comply with industry standards and promote device reliability.
Definition of Radiated Emissions
Radiated emissions refer to the unwanted electromagnetic energy that is emitted from electronic devices into the surrounding environment. This energy can travel through the air and affect other electronic devices, causing them to malfunction. The measurement of these emissions is vital in ensuring that devices operate within acceptable limits set by regulatory agencies and industry standards.
Types of Radiated Emissions Testing
There are various methods of conducting radiated emissions testing, typically categorized based on the frequency range and testing environment. Common types include:
- Open Area Test Site (OATS): This method involves testing in a controlled outdoor environment, providing minimal interference and allowing for accurate measurements.
- Semi-Anechoic Chamber: A specialized indoor facility that minimizes reflections of electromagnetic waves from the walls and ceiling but allows reflections from the floor to simulate the behavior of an OATS. These facilities are ideal for testing at higher ambient (noisy) areas where OATS testing is not possible due to interference from signals like radio, television, cell phone transmissions, and other unintentional emissions.
- Fully Anechoic Chamber: A highly controlled environment that eliminates reflections from all surfaces; allowing more accurate, repeatable and precise radiated emissions testing while reducing the uncertainty of the measurments.
Why is Radiated Emissions Testing Important?
The significance of radiated emissions testing extends beyond simple compliance; it plays a fundamental role in product design, user safety, and overall market success. Understanding the importance of this testing can help manufacturers prioritize EMC considerations early in the development process.
Impact on Electronic Devices
In today’s increasingly interconnected world, the reliability of electronic devices is paramount. Devices that fail radiated emissions testing may interfere with the functioning of critical equipment, leading to performance degradation or even total failure. This interference can have serious ramifications, particularly in industries such as healthcare, automotive, and telecommunications, where the stakes are high.
Compliance with Regulations
Manufacturers are legally obligated to ensure that their products comply with EMC regulations defined by various governmental and international bodies. Non-compliance can lead to significant penalties, including recalls, fines, and damage to company reputation. By conducting radiated emissions testing, manufacturers not only adhere to these regulations but also demonstrate a commitment to quality and safety in their products.
Testing Standards and Regulatory Requirements
Radiated emissions testing is governed by numerous standards and regulations that define acceptable limits for electromagnetic interference. Understanding these standards is vital for manufacturers aiming for compliance and successful product launches.
Overview of Testing Standards
Several key standards guide radiated emissions testing, including:
- FCC Part 15: The Federal Communications Commission (FCC) sets regulations for unintentional radiators in the United States.
- IEC 61000-6-3: This standard outlines general emission requirements for residential, commercial, and light industrial environments.
- EN 55032: This European standard specifies limits and methods of measurement for multimedia equipment.
Radiated Emissions Limits
Each regulatory standard sets specific limits for radiated emissions, typically defined in decibels (dBμV/m). These limits vary depending on the frequency range, the type of environment (residential, commercial, industrial), and the nature of the devices being tested. It is critical for manufacturers to familiarize themselves with these limits to ensure compliance.
Key Regulatory Bodies
Several organizations are responsible for establishing and enforcing radiated emissions standards, including:
- Federal Communications Commission (FCC): Oversees regulations in the United States.
- International Electrotechnical Commission (IEC): Develops international standards to ensure safety and efficiency.
- European Union (EU): Oversees regulations in the European Union.
How Radiated Emissions Testing is Conducted
Radiated emissions testing requires a systematic approach that includes preparation, equipment selection, and adherence to established procedures. The following sections detail the key components involved in conducting these tests.
Testing Environment Setup
Establishing a suitable testing environment is critical for accurate radiated emissions measurements. Factors such as background noise, reflections, and environmental interference must be minimized. Depending on the testing method selected, this could involve preparing an outdoor test site or setting up a specialized chamber.
Using an Open Area Test Site
Open Area Test Sites (OATS) are often preferred for their minimal interference and ability to simulate real-world conditions. The site must be chosen carefully, ensuring it is free from nearby structures and electrical noise. During testing, the device under test (DUT) is placed at a specified height and orientation, and measurements are taken using calibrated antennas at various distances.
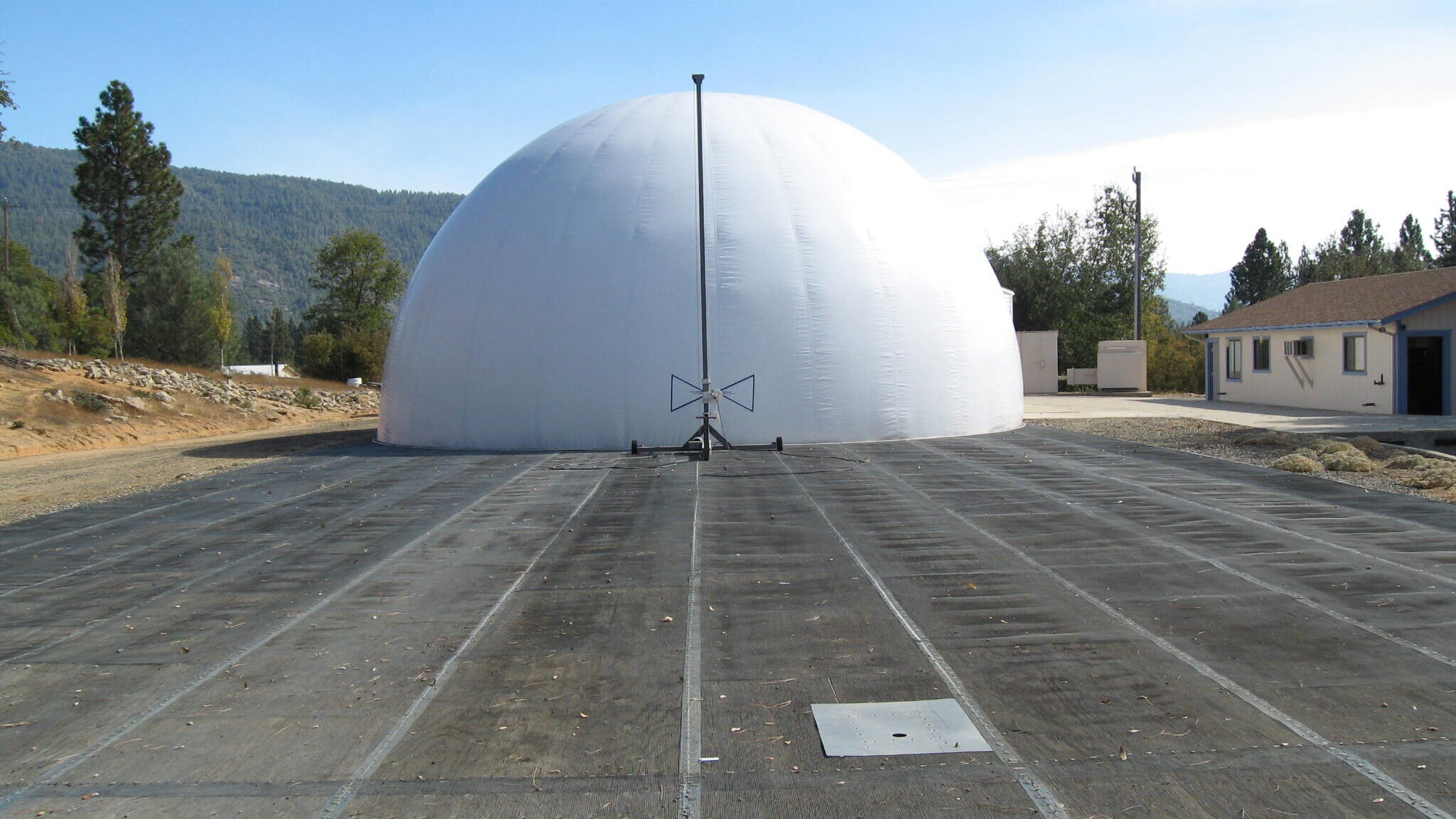
Equipment and Procedures
The equipment used in radiated emissions testing includes antennas, spectrum analyzers or receivers, pre-amplifiers, and various connectors and cables. The process typically involves:
- Setting the DUT to its operational state.
- Positioning antennas at designated angles and distances.
- Monitoring emissions across the relevant frequency range using a spectrum analyzer or receiver.
Data collected during testing is analyzed to determine if the emissions fall within acceptable limits defined by regulatory standards.
Common Causes of Radiated Emissions Failures
Understanding the common sources of radiated emissions failures can help manufacturers identify potential pitfalls during product design and testing. By addressing these issues, manufacturers can improve their devices’ chances of passing compliance testing.
Design Flaws
Poor design is one of the most significant contributors to excessive radiated emissions. Issues such as inadequate grounding, improper shielding, and the use of low-quality components can lead to increased electromagnetic interference. Manufacturers must prioritize thoughtful design practices and thorough reviews during the development process.
Component Issues
Individual components within a device can also lead to radiated emissions failures. For instance, switching power supplies, microcontrollers, and high-speed digital interfaces may generate unwanted emissions if not adequately managed. Selecting high-quality components and ensuring they are correctly integrated into the overall system can help mitigate these risks.
Environmental Factors
Environmental factors such as temperature and humidity can influence the performance of electronic devices. Devices tested in uncontrolled environments may exhibit different emission characteristics compared to those tested in controlled conditions. Therefore, manufacturers should consider environmental variables when conducting radiated emissions testing.
How to Reduce Radiated Emissions
Effective strategies for reducing radiated emissions should be integrated into the design and manufacturing processes. By prioritizing electromagnetic compatibility (EMC) from the outset, manufacturers can significantly enhance their products’ compliance prospects.
Best Practices for EMI Compliance Testing
Adhering to best practices during EMI compliance testing is essential for successful outcomes. This includes conducting preliminary tests during the design phase to identify potential issues early, maintaining proper documentation throughout the testing process, and ensuring that all equipment used is calibrated and functioning correctly.
Design Strategies for Reducing Emissions
Several design strategies can be employed to minimize radiated emissions:
- Use of Grounding Techniques: Effective grounding can help reduce emissions by providing a low-resistance path for unwanted signals.
- Shielding: Employing metal or conductive materials to shield sensitive components can significantly reduce EMI.
- PCB Layout Optimization: Designing printed circuit boards (PCBs) with careful consideration of trace routing and component placement can impact emission levels.
How to Reduce Radiated Emissions in Electronic Devices
In addition to design considerations, manufacturers can implement operational strategies to further reduce radiated emissions. This includes filtering techniques that limit the frequency content of signals, using twisted pair cables to minimize crosstalk, and ensuring proper cable management to avoid loops and unnecessary lengths.
Pre-Compliance Testing and Debugging
Pre-compliance testing is a proactive approach that allows manufacturers to identify and address potential issues before formal compliance testing. This phase is crucial for minimizing costs and time delays associated with failed tests.
Importance of Pre-Compliance Testing
Conducting pre-compliance tests helps manufacturers gain insights into their devices’ emission characteristics early in the development process. By identifying and rectifying issues before formal testing, manufacturers can avoid costly redesigns and expedite their time to market.
Best Practices for Effective Debugging
Effective debugging during the pre-compliance phase involves thorough analysis of emission data, iterative design improvements, and collaboration among engineering teams. Best practices include:
- Documentation of all test results and modifications made to the design.
- Regular communication among team members to share findings and solutions.
- Use of simulation tools to predict potential emission issues before physical testing.
Conclusion and FAQs
Understanding and conducting radiated emissions testing is vital for manufacturers looking to ensure the reliability and compliance of their electronic devices. By grasping the intricacies of emissions testing, adhering to standards, and implementing effective design strategies, manufacturers can avoid costly failures and achieve market readiness. As technology continues to evolve, the importance of EMC compliance will only increase, necessitating a commitment to quality and reliability.
Frequently Asked Questions (FAQs)
1. What is the difference between radiated emissions testing and conducted emissions testing?
Radiated emissions testing measures electromagnetic energy emitted into the air from a device, while conducted emissions testing measures electromagnetic interference traveling along power or signal lines.
2. How often should radiated emissions testing be conducted?
Manufacturers should conduct radiated emissions testing at various stages of product development, including pre-compliance tests during the design phase and formal compliance tests before market release.
3. What are the consequences of failing radiated emissions testing?
Failing radiated emissions testing can lead to regulatory penalties, product recalls, reputational damage, and increased development costs due to required redesigns.
4. Can design changes after initial testing affect radiated emissions?
Yes, any design changes, particularly those affecting circuit layout, grounding, or component selection, can significantly impact radiated emissions and should be re-evaluated through testing.
5. Do different countries have different radiated emissions standards?
Yes, various countries have established their own radiated emissions standards, which may differ in terms of limits and testing procedures. Compliance with local regulations is essential for market access.