Understanding Mechanical Testing
Mechanical testing is vital for ensuring that electronic devices can endure various real-world conditions and remain reliable. By subjecting devices to different types of stresses, both dynamic and environmental, manufacturers can identify weaknesses in their designs and make necessary improvements. Understanding mechanical testing will help engineers and designers make smart decisions earlier in the product development stages, reducing the need for costly, time consuming changes.
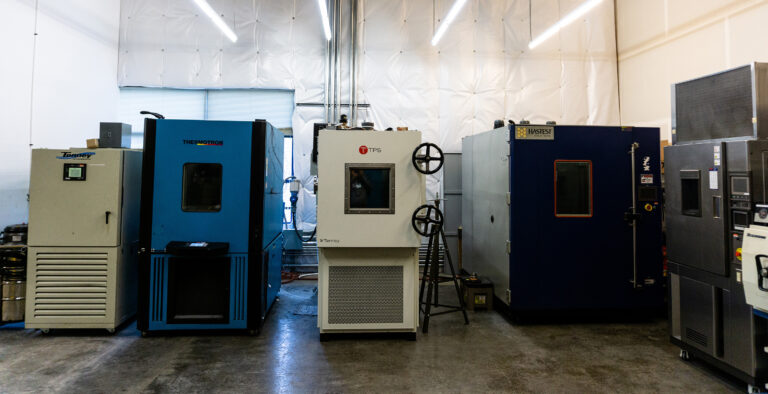
Types of Mechanical Tests Available
Some common types of mechanical tests include compression testing, acceleration testing, impact testing, and vibration testing. These tests help manufacturers understand how products will withstand various stresses during usage, transportation, and storage.
Environmental tests can simulate a variety of conditions a product might encounter. Test chambers are able to replicate extreme temperatures, humidity levels, and altitude scenarios. Salt fog chambers are available to recreate the harsh conditions encountered in a marine environment. Testing for water and dust ingress at varying temperatures and speeds can also be done. Understanding the types of testing available as well as the product being designed can help tailor test plans and avoid unnecessary overtesting.
Reliability Standards for Electronic Devices
Many industries rely on electronic devices to function properly without any issues and failures. To ensure these devices are reliable and meet safety standards, rigorous mechanical testing is essential. The reliability standards for electronic devices are established to guarantee that these devices can withstand various environmental conditions and usage scenarios. These standards are designed to:
- Test the durability of devices under different stress factors.
- Evaluate the ability of devices to perform consistently over time.
- Ensure that electronic devices meet safety regulations and are reliable in real-life situations.
Compliance with these reliability standards is critical for manufacturers to produce electronic devices that are safe, durable, and reliable for consumers.
Safety Considerations in Testing
In testing electronics for safety, it’s crucial to replicate real-life conditions to ensure the devices can withstand different scenarios. Here are some key safety considerations to keep in mind:
- Environmental Factors: Devices should be tested in extreme temperatures, humidity levels, and pressure parameters to simulate a range of conditions they may encounter.
- Impact Resistance: Testing for drop and impact resistance is important to assess how well the device can withstand accidental falls or rough handling.
- Electrical Safety: Insulation resistance, dielectric strength, and leakage current tests help evaluate the device’s ability to handle electrical stress without posing a safety hazard.
- Durability Testing: Assessing the device’s durability through repetitive use, bending, twisting, and other mechanical stress tests can reveal weak points that may lead to malfunctions or safety risks.
- Compliance Standards: Ensuring the testing procedures align with industry standards and regulations is essential to guarantee the device meets safety requirements.
By considering these factors during testing, manufacturers can enhance the safety and reliability of electronic devices for consumers.
Interpreting Test Results
Test results from mechanical testing for electronic safety and reliability are crucial for ensuring device durability. These results provide valuable insights into the performance and resilience of electronic components. Understanding and interpreting these test results accurately is vital for identifying potential weaknesses in the device design and improving its overall reliability. Pay close attention to testing variables, such as stress levels and failure modes, to optimize the device’s durability and safety standards.
Benefits of Rigorous Testing
Rigorous testing ensures that electronic devices are reliable and safe for consumers. By subjecting devices to various tests, manufacturers can identify weaknesses and potential failures before the products reach the market. This can help in improving the quality of devices and reducing the chances of malfunctions or hazards for users. Testing also allows manufacturers to meet industry standards and regulations, which is crucial for gaining consumer trust and confidence in the products.